The Future of Metalworking: Unpacking the Metalworking Fluids Market
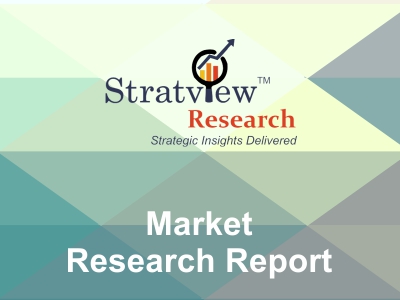
Metalworking forms the backbone of countless industries, shaping everything from the cars we drive to the buildings we inhabit. Metalworking fluids (MWFs) are the unsung heroes of this process, acting as coolants, lubricants, and corrosion inhibitors during various metalworking processes like cutting, grinding, and stamping. Understanding the future of MWFs is crucial for navigating the evolving landscape of metalworking.
Market Dynamics: Growth Trajectory and Key Drivers
According to Stratview Research, the global metalworking fluids market size was valued at USD 11.08 billion in 2022 and it is projected to reach USD 13.88 billion by 2028, growing at a CAGR of 3.77% during 2023-2028. This growth can be attributed to several key factors:
- Rise of Automotive and Heavy Machinery: The automotive industry's growing demand for lightweight and fuel-efficient vehicles necessitates the use of advanced MWFs during manufacturing. Similarly, the increasing requirement for heavy machinery in construction and other sectors fuels the demand for high-performance MWFs.
- Expanding Manufacturing Sector: The global manufacturing sector, particularly in regions like Asia Pacific, is experiencing significant growth. This translates to a higher demand for metalworking processes, consequently driving the MWFs market.
Shaping the Future: Trends at the Forefront
Several trends are influencing the metalworking fluids market, shaping its future course:
- Sustainability Imperative: Eco-Friendly Solutions Gain Traction Environmental regulations and a growing emphasis on sustainability are pushing manufacturers towards developing and using eco-friendly MWFs. These fluids are typically bio-based, readily biodegradable, and have lower toxicity levels, minimizing environmental impact during production, use, and disposal.
- Rise of Minimum Quantity Lubrication (MQL): MQL is a technique that utilizes minimal amounts of cutting fluid, delivering it directly to the cutting zone. This approach reduces fluid consumption, lowers disposal costs due to smaller volumes, and promotes a cleaner work environment with less mist and fog.
- Dry Machining: A Viable Alternative for Specific Applications Dry machining, which eliminates the use of MWFs altogether, is gaining traction in specific applications. This method is preferred for certain materials (like aluminum) and processes due to benefits like reduced environmental impact and improved surface finish, particularly for components requiring a pristine finish for further processing. However, dry machining may not be suitable for all scenarios due to limitations in cooling and lubrication, especially for high-friction processes.
- Multi-Phase MWFs: A New Generation of Performance Multi-phase MWFs are a new generation of fluids that offer superior performance compared to traditional options. These fluids combine different phases, such as oil and water, to provide enhanced cooling, lubrication, and corrosion protection while minimizing environmental hazards.
Delving Deeper: A Look at Different Types of Metalworking Fluids
MWFs come in various types, each suited for specific needs:
- Cutting fluids: Formulated to cool and lubricate the cutting tool and workpiece interface during machining processes like drilling, milling, and turning. They are further categorized into straight cutting oils, soluble oils, and synthetic cutting fluids, each offering different benefits in terms of cooling, lubrication, and anti-foaming properties.
- Grinding fluids: Designed for grinding operations to remove material and achieve desired surface finishes. They play a crucial role in preventing chip welding and ensuring operator safety by controlling dust generation. Grinding fluids can be water-based (synthetic or semi-synthetic) or oil-based depending on the material being ground.
- Forming fluids: Used during metal forming processes like stamping and pressing to reduce friction, prevent metal pickup on tools, and improve surface finish. They can be water-based, oil-based, or composed of special lubricants for specific forming operations.
- Machining coolants: Primarily water-based solutions used in conjunction with MQL technology. These coolants provide basic cooling and lubrication while minimizing fluid consumption.
Regional Landscape: A Geographical Perspective
The Asia Pacific region currently dominates the metalworking fluids market, accounting for a significant share due to the burgeoning manufacturing sector in countries like China and India. Government initiatives promoting domestic manufacturing further contribute to regional growth.
North America and Europe are also established markets for MWFs, although growth is expected to be slower compared to Asia Pacific. These regions may witness a shift towards more sustainable and MQL-compatible MWFs due to stricter environmental regulations.