Steel Forging Manufacturing Plant Project Report 2025: Project Report and Setup Guide
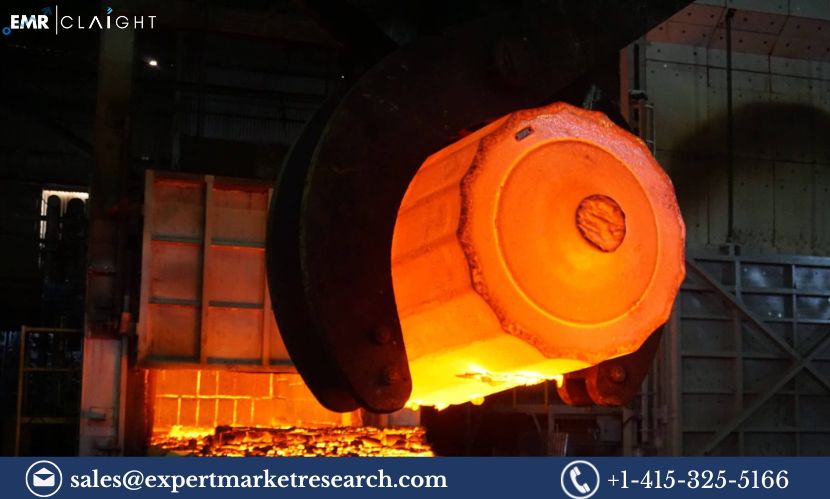
Introduction
Steel forging is a critical manufacturing process used to produce strong and durable steel components that are used in a wide variety of industries, including automotive, aerospace, construction, and heavy machinery. The process involves shaping steel through the application of high pressure and heat to form specific shapes and sizes that meet the demands of high-performance applications. With the increasing demand for high-quality forged steel components, the establishment of a steel forging manufacturing plant presents a significant business opportunity. This Steel Forging Manufacturing Plant Project Report outlines the feasibility, market potential, manufacturing process, plant setup, raw material procurement, regulatory compliance, and financial considerations for establishing a steel forging manufacturing plant. It provides comprehensive insights into the steps required to set up a successful plant and to ensure its operational success.
Market Overview
Global Steel Industry
The global steel industry is one of the largest and most vital sectors of the world economy, with steel being a fundamental material for numerous industries. Steel forging is a key subset of the steel industry, catering specifically to the production of components that require high strength, durability, and resilience. Industries such as automotive, aerospace, energy, and construction rely heavily on forged steel parts for critical applications.
The steel forging market has seen steady growth due to the following factors:
-
Industrialization and Infrastructure Development: The growth of manufacturing industries and infrastructure projects worldwide continues to drive demand for high-strength forged steel components used in machinery, tools, and equipment.
-
Automotive and Aerospace Industries: The demand for forged steel components in automotive and aerospace industries is increasing, as these industries require lightweight, high-strength materials for critical parts such as engine components, gears, axles, and structural elements.
-
Technological Advancements: Advancements in forging techniques and technologies, including precision forging and automation, have improved the quality, efficiency, and cost-effectiveness of steel forging processes, expanding their application across industries.
-
Energy and Heavy Machinery: The energy sector, particularly oil and gas, and heavy machinery manufacturing, require forged steel components that can withstand extreme conditions. Components such as valves, pumps, and turbine blades are critical to these industries.
Get a Free Sample Report with Table of Contents@
Key Applications of Steel Forging
Steel forgings are used in a wide range of applications where strength, durability, and reliability are paramount. Some of the key sectors and applications include:
-
Automotive Industry: Steel forgings are used in the production of critical components such as crankshafts, connecting rods, gears, axles, and suspension parts, all of which require high strength to ensure safety and performance.
-
Aerospace Industry: Forged steel components in aerospace are used for critical parts like turbine blades, landing gear, and engine components, which need to endure high pressure, extreme temperatures, and stress.
-
Construction and Heavy Equipment: Steel forgings are used in the production of parts for construction machinery, mining equipment, and industrial machinery. Components such as gears, shafts, and hydraulic valves are forged to handle high loads and extreme working conditions.
-
Energy Sector: Forged steel parts are used extensively in the oil and gas, power generation, and renewable energy sectors. These include components like valves, flanges, and pump casings used in oil rigs, power plants, and wind turbines.
-
Defense and Military: The defense industry requires high-strength forged steel parts for equipment such as tanks, artillery, and military vehicles.
Market Drivers
-
Growth in Manufacturing and Infrastructure: The continued development of infrastructure projects, particularly in emerging economies, is driving demand for durable, high-performance materials like forged steel.
-
Rising Demand for High-Performance Components: Industries such as automotive, aerospace, and energy require high-strength forged components that can withstand extreme conditions and maintain performance.
-
Technological Advancements in Forging: The implementation of advanced forging techniques, including hot and cold forging, and automation, is enhancing the efficiency of the forging process and improving product quality.
-
Increase in Industrial Applications: The growth of industries that require strong and durable parts, including machinery manufacturing, heavy equipment, and transportation, is a key driver for the steel forging market.
-
Government Initiatives and Regulations: Governments around the world are increasingly focusing on the development of heavy industries and renewable energy, both of which require forged steel components for machinery and infrastructure.
Market Challenges
While the steel forging market is growing, several challenges must be addressed for a successful plant operation:
-
High Capital Investment: Setting up a steel forging plant requires substantial capital investment in machinery, equipment, and infrastructure.
-
Energy Consumption: The steel forging process is energy-intensive, and managing energy consumption to maintain cost-efficiency and reduce environmental impact is a significant challenge.
-
Raw Material Costs: Fluctuating costs of raw materials such as steel can affect profitability, making it essential to have effective supply chain management and sourcing strategies.
-
Competition: The market for steel forgings is highly competitive, with many established players. New manufacturers must focus on quality, cost-efficiency, and technological innovation to differentiate themselves.
Feasibility Study for Setting Up a Steel Forging Manufacturing Plant
Site Selection and Infrastructure
The location of the steel forging manufacturing plant is crucial to ensure efficient operations. Factors to consider include:
-
Proximity to Raw Material Suppliers: The plant should be situated near suppliers of raw materials such as steel billets, which are essential for the forging process. Being located near steel mills or metal suppliers can help reduce transportation costs and ensure a steady supply of raw materials.
-
Access to Skilled Labor: Steel forging requires skilled workers who are proficient in operating complex machinery and adhering to quality standards. Choosing a location with access to a skilled workforce will improve operational efficiency.
-
Energy Availability: Steel forging is energy-intensive, requiring a consistent and affordable energy supply. The plant should be located in an area where energy resources are readily available and cost-effective.
-
Logistics and Transportation: The plant should have access to major transportation routes, such as highways and ports, to facilitate the movement of raw materials and finished products to and from the plant.
-
Regulatory and Environmental Compliance: The site must comply with local regulations related to industrial operations, including waste management, emissions control, and environmental protection. The plant should also be designed with energy efficiency and sustainability in mind.
Raw Material Procurement
The primary raw materials required for steel forging include:
-
Steel Billets: Steel billets are the starting material for the forging process. They are usually obtained from steel mills and come in various grades, depending on the end-use application of the forged parts.
-
Alloying Elements: Steel forgings often require additional alloying elements such as carbon, chromium, nickel, and molybdenum to achieve specific mechanical properties such as hardness, toughness, and resistance to wear.
-
Lubricants and Cooling Agents: Forging processes involve high temperatures, so lubricants and cooling agents are essential to reduce friction and prevent overheating of the equipment.
-
Energy and Gas: The forging process requires a significant amount of heat, which is typically generated by electric furnaces, gas furnaces, or induction heating systems. Access to reliable energy sources is crucial.
Manufacturing Process
The steel forging process involves several stages, which can vary depending on the specific type of forging required. The general process includes:
-
Heating: The raw steel billets are heated in a furnace to a high temperature to make them malleable and easier to shape. The heating process ensures that the steel can be forged into the desired shape without cracking.
-
Forging: The heated steel billets are placed into a die or mold and shaped using a mechanical or hydraulic press. The process can be done using various methods, including open-die forging, closed-die forging, and upset forging, depending on the complexity of the part.
-
Cooling: After the forging process, the steel components are cooled in a controlled manner to allow them to reach the required hardness and mechanical properties.
-
Machining and Finishing: Once the forged parts are cooled, they are subjected to machining processes such as turning, grinding, and drilling to achieve the final dimensions and surface finish.
-
Inspection and Quality Control: Steel forgings undergo rigorous testing and inspection to ensure that they meet the required mechanical properties, such as strength, hardness, and resistance to fatigue. Non-destructive testing methods such as ultrasonic testing and x-ray inspection are often used to detect internal defects.
-
Heat Treatment: Some steel forgings may require additional heat treatment processes such as quenching, tempering, or annealing to further improve their properties.
-
Packaging and Shipping: Once the forgings are complete, they are packaged carefully to prevent damage during transportation and shipped to customers.
Regulatory Compliance
Steel forging plants must comply with various local and international regulations, including:
-
Environmental Regulations: Steel forging operations must adhere to environmental standards, including waste management, emissions control, and energy consumption. Compliance with regulations such as ISO 14001 for environmental management is essential.
-
Health and Safety Standards: The manufacturing plant must implement safety protocols to protect workers from potential hazards, such as high temperatures, heavy machinery, and moving parts. Compliance with OSHA (Occupational Safety and Health Administration) regulations is mandatory.
-
Quality Standards: The plant should meet industry-specific quality standards, such as ISO 9001 for quality management and other certifications relevant to the steel forging industry.
Financial Considerations
Setting up a steel forging manufacturing plant involves substantial capital investment. Some of the key financial components include:
-
Initial Capital Investment: This includes the cost of land, facility construction, equipment, and machinery required for the forging process. Investment in high-tech forging presses, furnaces, and CNC machining equipment will be significant.
-
Operating Costs: These include raw material costs, energy consumption, labor costs, maintenance, and administrative expenses. Energy consumption is a key consideration, as steel forging is an energy-intensive process.
-
Revenue Generation: Revenue is primarily generated from the sale of forged steel components to industries such as automotive, aerospace, construction, and energy.
-
Profitability: The profitability of the plant will depend on production efficiency, product quality, market demand, and competitive pricing.
Marketing and Sales Strategy
-
Brand Development: Establish a strong brand that emphasizes high-quality, durable, and reliable forged steel components.
-
Target Market: Focus on industries such as automotive, aerospace, heavy machinery, energy, and construction that require forged steel parts for their operations.
-
Sales Channels: Develop relationships with original equipment manufacturers (OEMs), suppliers, distributors, and direct customers in the target markets.
-
Customer Support: Offer technical support, warranty services, and timely delivery to build customer loyalty and maintain long-term relationships.
Explore More Report
https://www.expertmarketresearch.com/articles/top-silica-sand-companies
Media Contact
Company Name: Claight Corporation
Contact Person: Peter Fernandas, Corporate Sales Specialist — U.S.A.
Email: sales@expertmarketresearch.com
Toll Free Number: +1–415–325–5166 | +44–702–402–5790
Address: 30 North Gould Street, Sheridan, WY 82801, USA
Website: www.expertmarketresearch.com
Aus Site: https://www.expertmarketresearch.com.au