Nous rejoindre
Connexion S’enregistrerEvènements
Blogs
Marketplace
Groupes
Pages
Lire la suite
Evènements Emplois Offres
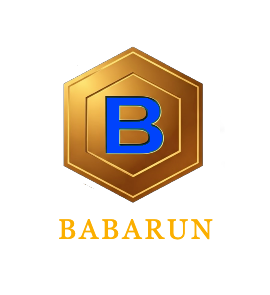
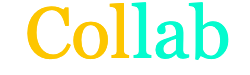
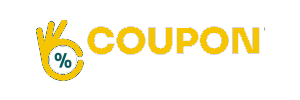
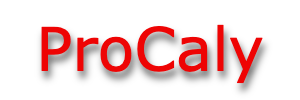
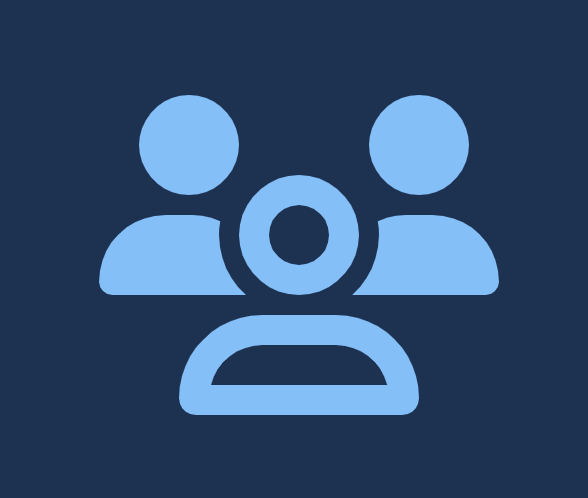

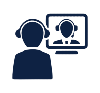
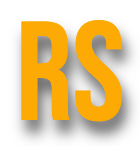
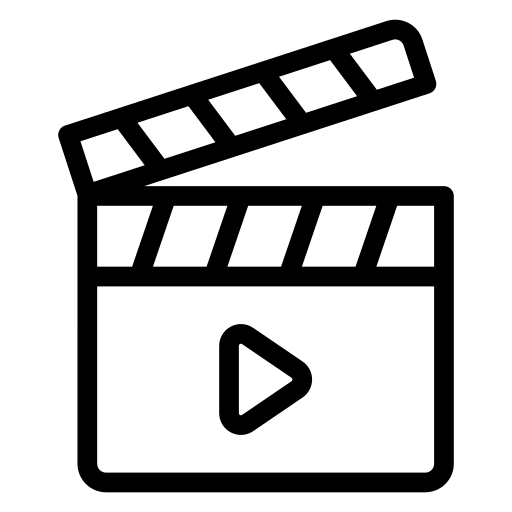
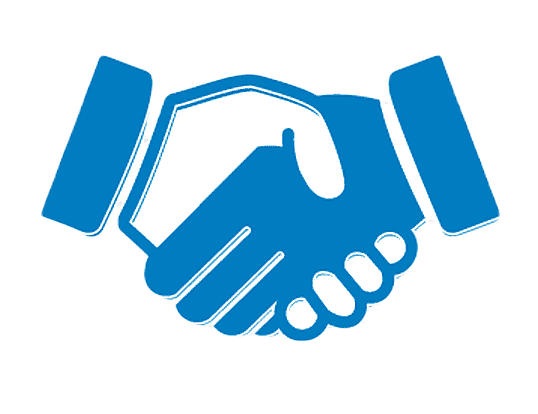
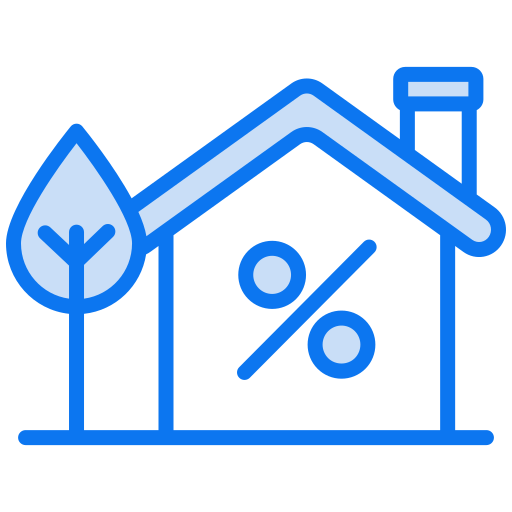
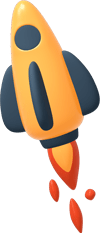
Mise à niveau vers Pro
High-Density Fiberboard (HDF) Manufacturing Plant Project Report 2025: Project Report and Setup Guide
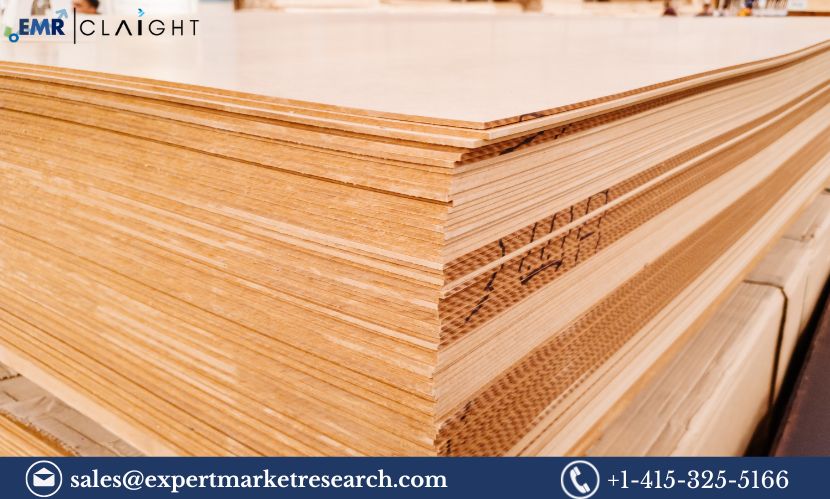
Introduction
The High-Density Fiberboard (HDF) Manufacturing Plant Project Report is designed to provide a detailed and comprehensive understanding of setting up a manufacturing plant dedicated to the production of HDF. High-Density Fiberboard is a versatile and durable engineered wood product made from wood fibers and adhesives. It is widely used in furniture manufacturing, flooring, construction, and automotive industries due to its strength, smooth surface, and affordability.
The growing demand for HDF, coupled with the increasing need for sustainable and eco-friendly building materials, has spurred interest in HDF manufacturing. This project report outlines the entire process, including market trends, raw material sourcing, plant design, production technology, cost estimation, and financial projections. By investing in an HDF manufacturing plant, businesses can tap into the rising demand for high-quality engineered wood products.
Market Overview and Demand Analysis
The global market for HDF is expected to grow steadily due to its wide range of applications in furniture, flooring, construction, and other sectors. As the demand for sustainable and cost-effective building materials rises, HDF has gained popularity for its environmental benefits and superior performance.
Key Drivers of HDF Demand
-
Furniture Industry: The demand for HDF in the furniture industry is significant, as it is used for producing laminated furniture, panels, and other products. Its smooth surface, durability, and cost-effectiveness make it a popular choice for manufacturing flat-pack furniture, cabinets, and tables.
-
Flooring: HDF is also widely used in flooring applications, particularly in laminate flooring. HDF's resistance to moisture, durability, and ease of maintenance have led to its increasing adoption in both residential and commercial flooring.
-
Construction Industry: The demand for HDF in the construction industry is driven by its use in wall panels, door cores, and insulation boards. The increasing need for energy-efficient, durable, and affordable materials in modern buildings contributes to HDF's growing popularity.
-
Automotive Industry: HDF is used in the automotive sector for interior applications such as door panels, dashboards, and flooring. The lightweight and durable nature of HDF makes it an attractive choice for reducing vehicle weight and enhancing performance.
-
Eco-friendly Building Materials: As consumers and industries are becoming more eco-conscious, the demand for sustainable and renewable materials has increased. HDF, being made primarily from wood fibers, is considered an environmentally friendly alternative to solid wood.
Get a Free Sample Report with Table of Contents@
Site Selection and Location
Choosing the right location for an HDF manufacturing plant is crucial for ensuring smooth operations and profitability. Factors such as raw material availability, transportation access, labor supply, and regulatory considerations must be taken into account.
Key Considerations for Site Selection
-
Proximity to Raw Materials: The primary raw material for HDF production is wood fibers, which are often sourced from timber mills, sawmills, and recycled wood. The plant should be located close to these suppliers to minimize transportation costs and ensure a consistent supply of raw materials.
-
Transportation and Logistics: The plant should be situated in an area with good transportation infrastructure, including access to highways, railways, or ports. This ensures that both raw materials and finished products can be easily transported.
-
Energy Supply: HDF production requires significant energy for processes such as fiber drying and bonding. Access to reliable and affordable energy sources is essential for maintaining cost-effective operations.
-
Labor Availability: The manufacturing plant will need skilled workers, including machine operators, maintenance technicians, and quality control personnel. Locating the plant in an area with a sufficient labor pool is important for staffing the facility.
-
Regulatory Compliance: The plant must comply with local regulations regarding environmental standards, labor laws, and safety protocols. Choosing a location with favorable regulatory conditions can reduce the risk of delays in permits and approvals.
Plant Design and Infrastructure
The design and infrastructure of the HDF manufacturing plant should focus on optimizing production efficiency, safety, and product quality. The plant layout should be designed to accommodate raw material handling, production processes, and finished product storage while ensuring smooth workflows and compliance with safety regulations.
Key Areas of the Plant Layout
-
Raw Material Storage: A dedicated area for storing wood fibers and adhesives, ensuring proper storage conditions to prevent contamination and degradation of materials.
-
Fiber Preparation: This section is where wood fibers are processed, refined, and prepared for bonding. It includes equipment such as shredders, grinders, and drying systems.
-
Forming and Pressing Area: This is the core production area where the wood fibers are mixed with resins and adhesives and then pressed into sheets to form the HDF panels. Hydraulic presses, forming machines, and drying ovens are used in this process.
-
Cooling and Cutting Area: After pressing, the HDF panels must be cooled and cut into the required sizes. Cutting machines and conveyors are used to handle the panels and ensure they meet the desired dimensions.
-
Finishing and Quality Control: The finished HDF panels undergo surface finishing, including sanding and coating, to improve appearance and durability. The quality control area is responsible for inspecting the panels for defects and ensuring that they meet industry standards.
-
Packaging and Dispatch: Once the HDF panels have passed quality control, they are packaged for shipment. Packaging machines, stacking systems, and storage areas are used to prepare the products for distribution.
Production Process
The production of High-Density Fiberboard (HDF) involves several key steps, from raw material preparation to finishing and packaging. Below is an overview of the typical production process:
Step 1: Raw Material Preparation
Wood chips or sawdust are sourced from timber mills and sawmills and are processed into fibers. The raw material is shredded into fine wood fibers, which are then dried to reduce moisture content.
Step 2: Fiber Bonding
The wood fibers are mixed with resin or adhesives to create a composite material. The resin bonds the fibers together and gives the HDF its strength and durability. The mixture may also include additives such as fire retardants, moisture resistance agents, and colorants.
Step 3: Forming the Panel
The fiber-resin mixture is spread onto a large conveyor belt or mold, and it is formed into sheets of the desired thickness. These sheets are then subjected to high pressure in hydraulic presses, which compress the fibers and resin to form a solid panel.
Step 4: Drying
After pressing, the HDF panels are dried in large drying ovens or kilns to remove any excess moisture. This step is essential to ensure that the panels do not warp or shrink after production.
Step 5: Cooling and Cutting
Once the HDF panels are dry, they are cooled to room temperature. The cooled panels are then cut into specific dimensions using cutting machines or saws. These panels can be further processed based on customer requirements.
Step 6: Finishing and Quality Control
The HDF panels undergo finishing processes such as sanding and coating to enhance their appearance and durability. The panels are then inspected for defects, and only those that meet quality standards are packaged for shipment.
Step 7: Packaging and Dispatch
The finished panels are carefully packaged and labeled for shipment. The packaging is designed to protect the panels from damage during transportation. The products are then dispatched to distributors, retailers, or directly to customers.
Financial Analysis and Cost Estimation
Starting a High-Density Fiberboard manufacturing plant requires a significant capital investment. A comprehensive financial analysis is essential to estimate the total cost of setting up the plant and assess its profitability.
Capital Expenditure (CAPEX)
- Land and Building: The cost of acquiring land and constructing the manufacturing facility.
- Machinery and Equipment: Investment in equipment such as wood fiber grinders, hydraulic presses, drying ovens, cutting machines, and packaging systems.
- Raw Materials: Initial procurement of wood fibers, resins, adhesives, and additives.
- Safety and Environmental Compliance: Investment in safety systems, waste management solutions, and compliance with environmental regulations.
Operating Expenditure (OPEX)
- Raw Material Costs: Ongoing costs of sourcing wood fibers, resins, and additives for production.
- Labor Costs: Salaries for machine operators, maintenance staff, quality control personnel, and administrative workers.
- Energy Costs: The plant will require significant energy for heating, pressing, and drying processes.
- Maintenance Costs: Regular maintenance and repairs for machinery and equipment.
- Logistics and Distribution: Costs associated with packaging, storage, and transportation of finished products.
Profitability and Break-even Analysis
The break-even point is a critical consideration for any manufacturing plant. By analyzing fixed costs, variable costs, and production capacity, businesses can determine the number of HDF panels that need to be produced and sold to cover initial investments and operating expenses.
Related Reports
https://www.expertmarketresearch.com/articles/top-washing-machine-companies
Media Contact
Company Name: Claight Corporation
Contact Person: Peter Fernandas, Corporate Sales Specialist
Email: sales@expertmarketresearch.com
Toll Free Number: +1–415–325–5166 | +44–702–402–5790
Address: 30 North Gould Street, Sheridan, WY 82801, USA
Website: www.expertmarketresearch.com